In the field of sheet metal processing, cost control is a key factor in improving the competitiveness of enterprises. Whether it is medical sheet metal processing or precision sheet metal manufacturing, reducing costs while ensuring product quality is the top priority. Let's analyze the cost reduction strategy of sheet metal processing from the two aspects of material selection and process optimization.
Material selection and cost reduction
- Understand material properties and prices: Different sheet metal materials have different properties and prices. Common ones are ordinary carbon steel, stainless steel, aluminum alloy, etc. In the processing of medical product parts, if the corrosion resistance of the material is not high, ordinary carbon steel with a relatively low price can be used instead of stainless steel to reduce material costs while meeting basic use needs. Aluminum alloys are widely used in some sheet metal chassis processing scenarios with weight requirements due to their light weight and high strength. Although the unit price may be higher than that of ordinary carbon steel, considering its performance advantages, it can sometimes reduce the overall cost.
- Reasonable selection of material specifications: In sheet metal processing plants, reasonable selection of material specifications according to actual processing needs can also effectively reduce costs. Avoid using materials of too large specifications to cause unnecessary waste. For example, for the processing of small medical device accessories, the required material size is accurately calculated, and plates of appropriate width and length are selected to reduce the generation of scraps and improve material utilization.
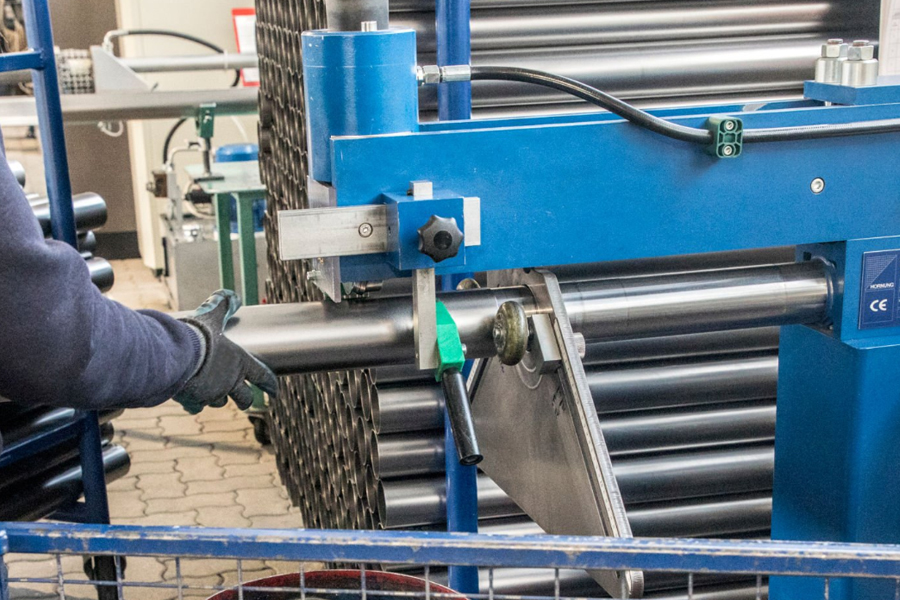
Process optimization and cost reduction
- Optimize processing technology: Laser sheet metal processing is an efficient processing method, but different processing parameters will affect the processing cost. Reasonable setting of parameters such as laser power and cutting speed can not only ensure processing quality, but also improve processing efficiency and reduce processing costs per unit time. For some sheet metal parts with complex shapes, a composite process combining punching and bending may be more economical and efficient than single laser cutting.
- Equipment and mold selection: It is also crucial to choose suitable processing equipment and molds. Although advanced automation equipment has a large initial investment, it can improve production efficiency and reduce labor costs in long-term large-scale production. When performing sheet metal processing, standard molds or customized molds are selected according to different processing requirements. For mass-produced products, although customized special molds have a high initial investment, they can improve production accuracy and efficiency, and reduce costs in the long run; for small batch and multi-variety production, it is more economical to use standard molds.
- Reduce processing steps: Under the premise of ensuring product quality, simplify the processing steps as much as possible. For example, in the processing of medical parts, through optimized design, sheet metal parts that originally required multiple processes to complete are merged into fewer processes, reducing processing time and labor costs.
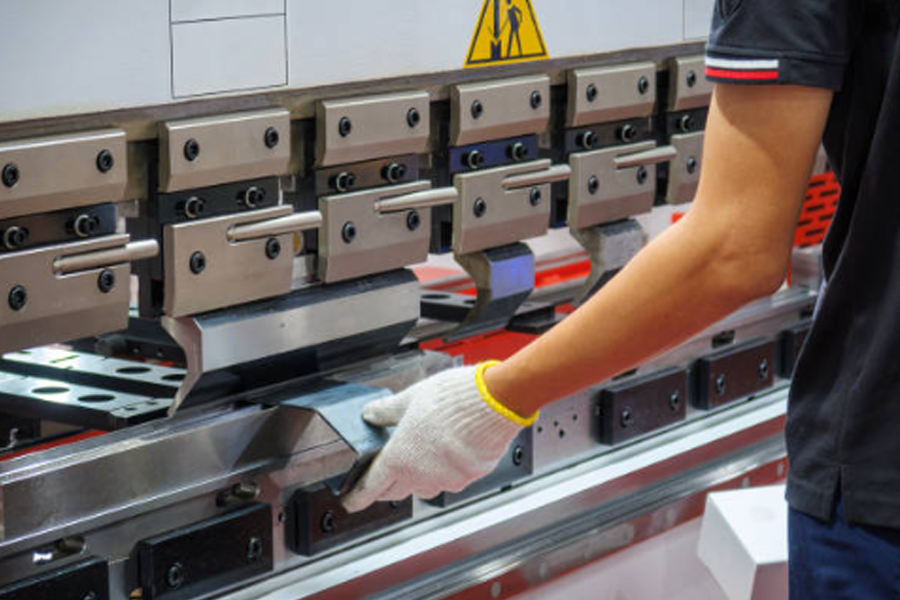
The control of sheet metal processing costs is a comprehensive process, from the careful calculation of material selection to the step-by-step process optimization, each link is closely connected. Through reasonable material selection and process optimization, enterprises can effectively reduce costs and improve market competitiveness when conducting sheet metal processing, medical sheet metal processing, precision sheet metal manufacturing and other businesses.