With the trend of detailed division of labor in the manufacturing industry, OEM (original equipment manufacturing) and ODM (design and manufacturing) services in the field of sheet metal processing have gradually become important choices for enterprises to optimize resource allocation. This cooperation model is not only about the transfer of production capacity, but also involves system engineering such as technical standard docking, process adaptation optimization, and quality system integration.
The core difference between OEM and ODM
- OEM model: Based on the complete technical information provided by the customer (including drawings, BOM lists, and process specifications), the foundry strictly performs production according to the standards. This model is suitable for companies with mature product designs. The core value of the foundry lies in the cost control and quality control capabilities in large-scale production.
- ODM model: The customer proposes functional requirements and performance indicators, and the foundry completes the entire process of structural design, material selection, and process development. This model is common in scenarios that require rapid response to the market, and tests the foundry's interdisciplinary design capabilities and industry experience accumulation.
The essential difference between the two models lies in the ownership of intellectual property rights - OEM product technology belongs to the customer, and ODM solutions are usually patented by the foundry.
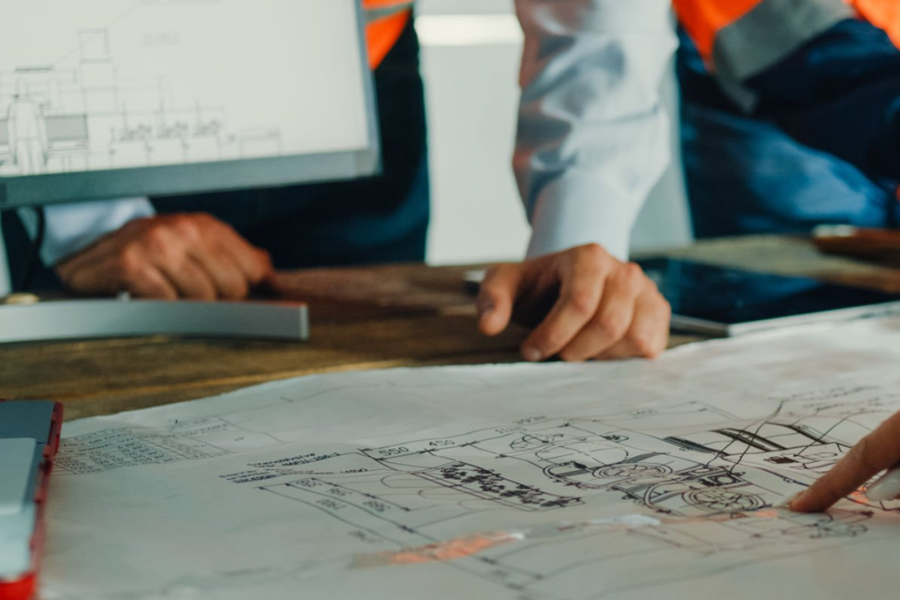
Collaborative optimization in the design stage
Professional foundries start to intervene in technical optimization at the drawing conversion stage:
- Tolerance rationality verification: adjust the tolerance band according to the equipment processing accuracy, for example, the linear tolerance of laser cutting is recommended to be relaxed to ±0.1mm (the scrap rate increases by 12% when the original design is ±0.05mm).
- Process feasibility assessment: identify the processing difficulties in the design, such as complex structures with more than 5 consecutive bends, which require the splitting of welding components or the increase of process gaps.
- Material utilization rate improvement: Through the intelligent layout software to optimize the plate cutting path, the conventional utilization rate of 6mm thick Q235 steel plate can be increased from 68% to 82%.
Experienced engineers will simultaneously consider the needs of subsequent processes, such as reserving hanging points for sprayed parts to avoid manual re-hanging in the later stage to affect the coating quality.
Technical adaptation of production links
The core competitiveness of foundries is reflected in the conversion of general equipment into dedicated production capacity:
- Flexible production line configuration: For small batch orders of multiple varieties, a modular fixture system is used, and the adjustment time when switching products can be controlled within 30 minutes.
- Construction of process parameter library: Establish a processing parameter matrix of different materials, thicknesses and structures. For example, the laser cutting speed of 1.5mm stainless steel sheet is recommended to be set to 6m/min and the nitrogen pressure is 0.8MPa.
- Process error prevention mechanism: Set up a laser projection positioning system in the bending process to transform the traditional tool setting process that relies on workers' experience into a visual operation, shortening the training cycle for new employees by 60%.
Real-time collection of equipment status data through the MES system can provide early warning of potential risks such as tool wear and positioning offset, and control the probability of batch quality accidents below 0.3%.
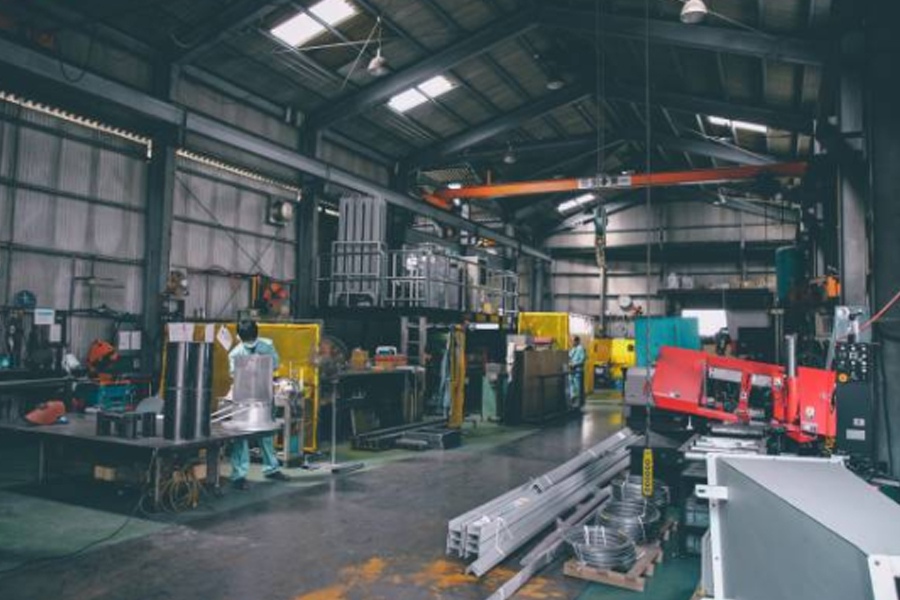
System integration of quality control
Mature OEM factories need to achieve compatibility between customer standards and their own systems:
- Unified testing benchmarks: Coordinate the coordinate system settings of the three-coordinate measuring machines of both parties to ensure the comparability of cross-factory testing data.
- Special feature management: Identify key features in customer products (such as the flatness of waterproof cabinets ≤0.5mm/m) and set up independent control charts for process monitoring.
- Traceability system docking: Laser marking or RFID tags are used to achieve full-process traceability of a single product from raw material batches to shipment inspection.
Deep collaboration of the supply chain
The value of ODM service providers extends to the supply chain management link:
- Cost optimization plan: Reduce overall costs through material substitution, such as using DX53D+Z galvanized sheet to replace traditional SPCC cold-rolled sheet, saving 15% of material costs under the same corrosion resistance requirements.
- Secondary supplier management: Establish a list of qualified suppliers for purchased parts such as fasteners and sealing strips, and require key component suppliers to provide CPK process capability analysis reports.
- Inventory strategy customization: For long-cycle raw materials (such as special specification aluminum plates), implement the VMI supplier management inventory model to increase customer inventory turnover to 8-10 times per year.
Technical closed loop of after-sales support
Professional service providers should establish full life cycle support capabilities:
- Process knowledge transfer: Provide "Key Process Control Points" simultaneously when delivering products to guide customers to install and maintain.
- Failure analysis support: Equipped with metallographic microscopes, salt spray test chambers and other equipment to assist customers in analyzing the root causes of corrosion, deformation and other problems of failed parts on site.