Con la tendencia de una división refinada del trabajo en la industria manufacturera, los servicios OEM (fabricación de equipos originales) y ODM (diseño y fabricación) en el campo del procesamiento de chapa metálica se han convertido gradualmente en una opción importante para que las empresas optimicen la asignación de recursos. Este modelo de cooperación no solo se refiere a la transferencia de capacidad de producción, sino que también incluye la ingeniería de sistemas como la armonización de normas técnicas, la adaptación y optimización de procesos y la integración de sistemas de calidad.
La diferencia fundamental entre OEM y ODM
- Modelo OEM: Basándose en la información técnica completa proporcionada por el cliente (incluidos dibujos, listas de materiales, especificaciones del proceso), la fundición lleva a cabo la producción estrictamente de acuerdo con los estándares. Este modelo es adecuado para empresas que ya cuentan con diseños de productos consolidados. El valor fundamental de la fundición reside en su capacidad de control de costes y calidad en la producción a gran escala.
- Modelo ODM: El cliente propone requisitos funcionales e indicadores de rendimiento, y la fundición completa todo el proceso de diseño estructural, selección de materiales y desarrollo del proceso. Este modelo es común en escenarios que requieren una respuesta rápida al mercado y pone a prueba las capacidades de diseño interdisciplinario de la fundición y la experiencia acumulada en la industria.
La diferencia esencial entre ambos modelos radica en la titularidad de los derechos de propiedad intelectual: la tecnología del producto OEM pertenece al cliente y las soluciones ODM suelen estar patentadas por la fundición.
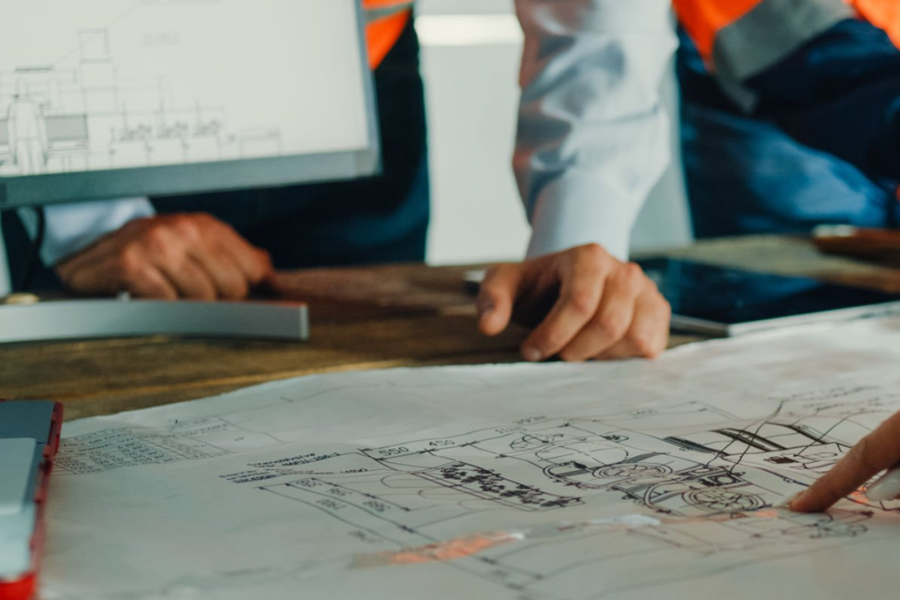
Optimización colaborativa en la fase de diseño
Las fundiciones profesionales comienzan a optimizar la tecnología en la etapa de conversión del dibujo:
- Verificación de la racionalidad de la tolerancia: ajuste la banda de tolerancia según la precisión de procesamiento del equipo. Por ejemplo, se recomienda reducir la tolerancia lineal del corte láser a ±0,1 mm (la tasa de desperdicio aumenta un 12 % cuando el diseño original es de ±0,05 mm).
- Evaluación de viabilidad del proceso: identificar dificultades de procesamiento en el diseño, como estructuras complejas con más de 5 curvas consecutivas, que requieren la división de componentes soldados o el aumento de espacios en el proceso.
- Utilización mejorada del material: al optimizar la ruta de corte de la placa a través de un software de anidamiento inteligente, la tasa de utilización convencional de la placa de acero Q235 de 6 mm de espesor se puede aumentar del 68% al 82%.
Los ingenieros experimentados también considerarán los requisitos de los procesos posteriores, como reservar puntos de suspensión para las piezas pulverizadas para evitar tener que volver a colgarlas manualmente, lo que afecta la calidad del recubrimiento.
Adaptación técnica en la producción
La principal competitividad de las fundiciones reside en convertir equipos de uso general en capacidades de producción especializadas:
- Configuración flexible de la línea de producción: para pedidos de lotes pequeños de múltiples variedades, se adopta un sistema de fijación modular y el tiempo de ajuste al cambiar de producto se puede controlar en 30 minutos.
- Construcción de la biblioteca de parámetros de proceso: Establecer una matriz de parámetros de procesamiento para diferentes materiales, espesores y estructuras. Por ejemplo, se recomienda ajustar la velocidad de corte por láser de una placa de acero inoxidable de 1,5 mm a 6 m/min y la presión de nitrógeno a 0,8 MPa.
- Mecanismo de prevención de errores de proceso: Se instala un sistema de posicionamiento por proyección láser en el proceso de doblado para transformar el proceso tradicional de ajuste de herramientas que se basa en la experiencia de los trabajadores en una operación visual, acortando el período de capacitación para los nuevos empleados en un 60%.
Al recopilar datos sobre el estado del equipo en tiempo real a través del sistema MES, se pueden advertir con antelación riesgos potenciales como el desgaste de las herramientas y la desviación de posicionamiento, y se puede controlar la probabilidad de accidentes de calidad del lote por debajo del 0,3 %.
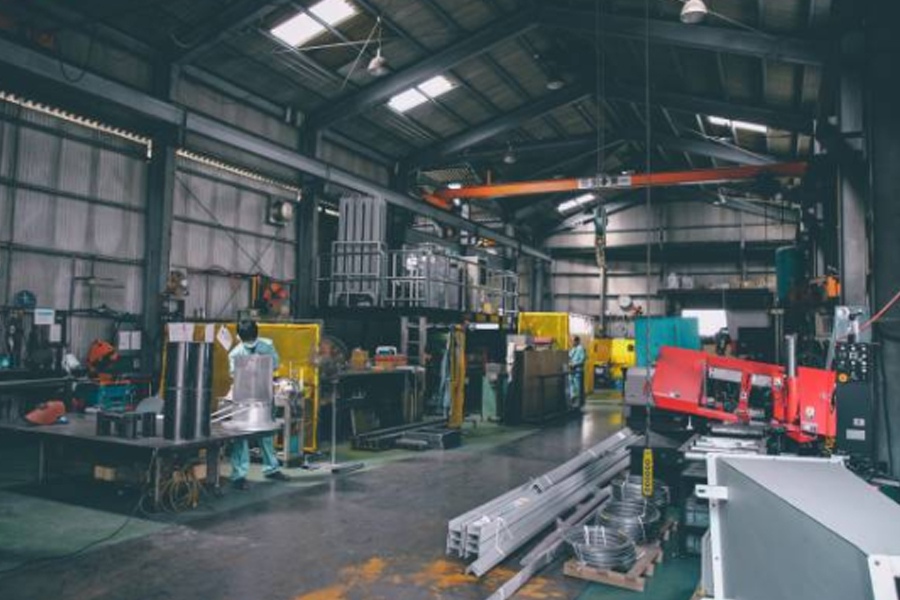
Integración del sistema de control de calidad
Una fundición madura necesita lograr la compatibilidad entre los estándares del cliente y su propio sistema:
- Punto de referencia de prueba unificado: coordine las configuraciones del sistema de coordenadas de las máquinas de medición de coordenadas tridimensionales de ambas partes para garantizar la comparabilidad de los datos de pruebas entre fábricas.
- Gestión de características especiales: identificar características clave en los productos del cliente (como la planitud del gabinete a prueba de agua ≤ 0,5 mm/m) y configurar gráficos de control independientes para el monitoreo del proceso.
- Conexión del sistema de trazabilidad: El marcado láser o las etiquetas RFID se utilizan para lograr la trazabilidad de todo el proceso de un solo producto, desde el lote de materia prima hasta la inspección del envío.
Colaboración profunda de la cadena de suministro
El valor de los proveedores de servicios ODM se extiende a la gestión de la cadena de suministro:
- Solución de optimización de costos: Reduzca los costos generales mediante la sustitución de materiales. Por ejemplo, el uso de chapa galvanizada DX53D+Z en lugar de la chapa laminada en frío SPCC tradicional puede ahorrar un 15 % en costos de material con los mismos requisitos de resistencia a la corrosión.
- Gestión de proveedores de segundo nivel: establecer una lista de proveedores calificados para las piezas compradas, como sujetadores y tiras de sellado, y exigir a los proveedores de componentes clave que proporcionen informes de análisis de capacidad del proceso CPK.
- Personalización de la estrategia de inventario: para materias primas de ciclo largo (como placas de aluminio con especificaciones especiales), implementamos el modelo de inventario de gestión de proveedores VMI para aumentar la tasa de rotación de inventario de los clientes a 8-10 veces al año.
Circuito cerrado técnico de soporte posventa
Los proveedores de servicios profesionales deben establecer capacidades de soporte durante todo el ciclo de vida:
- Transferencia de conocimiento del proceso: Al entregar los productos, proporcionaremos "Puntos clave de control del proceso" para guiar a los clientes en la instalación y el mantenimiento.
- Soporte de análisis de fallas: Equipado con microscopios metalográficos, cámaras de prueba de niebla salina y otros equipos para ayudar a los clientes a analizar las causas fundamentales de la corrosión, la deformación y otros problemas de las piezas fallidas en el sitio.