在制造业分工细化的趋势下,钣金加工领域的 OEM(代工生产)和 ODM(设计制造)服务逐渐成为企业优化资源配置的重要选择。这种合作模式不仅关乎生产能力的转移,更涉及技术标准对接、工艺适配优化、质量体系融合等系统工程。
一、OEM 与 ODM 的核心差异
- OEM 模式:基于客户提供的完整技术资料(包括图纸、BOM 清单、工艺规范),代工厂严格按标准执行生产。此模式适用于已有成熟产品设计的企业,代工厂的核心价值在于规模化生产中的成本控制与品控能力。
- ODM 模式:客户提出功能需求与性能指标,由代工厂完成结构设计、材料选型、工艺开发全流程。此模式常见于需要快速响应市场的场景,考验代工厂的跨学科设计能力与行业经验积累。
两种模式的本质区别在于知识产权归属 ——OEM 产品技术归属客户,ODM 方案通常由代工厂持有专利。
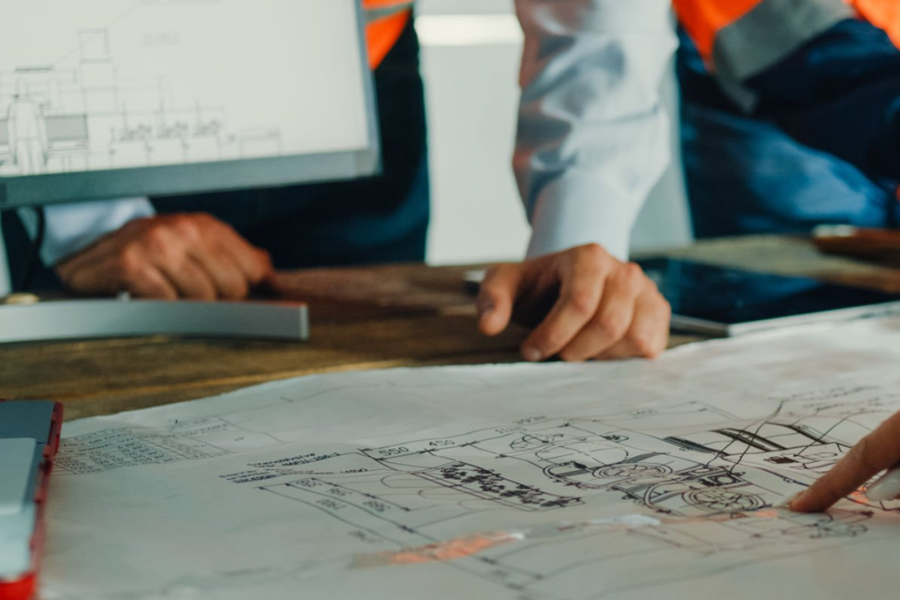
二、设计阶段的协同优化
专业代工厂在图纸转化阶段即开始介入技术优化:
- 公差合理性验证:根据设备加工精度调整公差带,例如激光切割的线性公差建议放宽至 ±0.1mm(原设计 ±0.05mm 时废品率增加 12%)。
- 工艺可行性评估:识别设计中的加工难点,如连续折弯次数超过 5 次的复杂结构,需拆分焊接组件或增加工艺缺口。
- 材料利用率提升:通过智能排样软件优化板材切割路径,6mm 厚 Q235 钢板的常规利用率可从 68% 提升至 82%。
经验丰富的工程师会同步考虑后续工序需求,例如喷涂件预留挂点位置,避免后期手工补挂影响涂层质量。
三、生产环节的技术适配
代工厂的核心竞争力体现在将通用设备转化为专用生产能力:
- 柔性化产线配置:针对多品种小批量订单,采用模块化夹具系统,切换产品时调整时间可控制在 30 分钟内。
- 工艺参数库建设:建立不同材料 - 厚度 - 结构的加工参数矩阵,例如 1.5mm 不锈钢板材的激光切割速度建议设定为 6m/min,氮气压力 0.8MPa。
- 过程防错机制:在折弯工序设置激光投影定位系统,将传统依赖工人经验的对刀过程转化为可视化操作,新人培训周期缩短 60%。
通过 MES 系统实时采集设备状态数据,可提前预警刀具磨损、定位偏移等潜在风险,将批量性质量事故概率控制在 0.3% 以下。
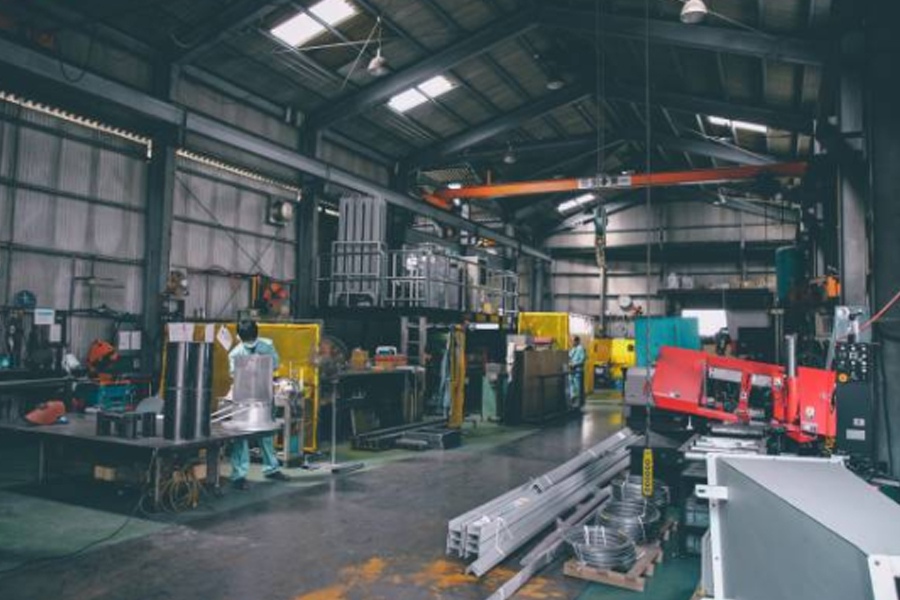
四、质量管控的体系融合
成熟的代工厂需实现客户标准与自有体系的兼容:
- 检测基准统一:协调双方三坐标测量机的坐标系设定,确保跨厂检测数据可比性。
- 特殊特性管理:识别客户产品中的关键特性(如防水柜体的平面度≤0.5mm/m),设置独立控制图进行过程监控。
- 追溯系统对接:采用激光打标或 RFID 标签,实现单件产品从原材料批次到出货检验的全流程追溯。
五、供应链的深度协同
ODM 服务商的价值延伸至供应链管理环节:
- 成本优化方案:通过材料替代降低综合成本,例如采用 DX53D+Z 镀锌板替代传统 SPCC 冷轧板,在同等耐蚀性要求下节约材料成本 15%。
- 二级供应商管理:建立紧固件、密封胶条等外购件的合格供应商名录,要求关键部件供应商提供 CPK 过程能力分析报告。
- 库存策略定制:对于长周期原材料(如特殊规格铝板),实施 VMI 供应商管理库存模式,将客户库存周转率提升至每年 8-10 次。
六、售后支持的技术闭环
专业服务商应建立全生命周期支持能力:
- 工艺知识传递:交付产品时同步提供《关键工序控制要点》,指导客户进行安装维护。
- 失效分析支持:配备金相显微镜、盐雾试验箱等设备,协助客户分析现场失效件的腐蚀、变形等问题根源。